Содержание
- Процесс диспергирования
- Эффект Doughnut
- Принцип работы фрезы по разрушению агломерированных твердых компонентов смеси
- Принцип работы фрезы и оптимизация состава смеси
- Перенос лабораторных результатов в производственные условия
- Окружная скорость вращения в зависимости от числа оборотов и диаметра фрезы
- Что следует предпринять, если не достигнут желаемый эффект диспергирования?
- Реологические свойства смеси
- Диспергирование в вакууме
Диспергирование в лаборатории, исследовательских цехах и производстве с диссольверами DISPERMAT®
1. Процесс диспергирования
Основной задачей диссольвера является распределение твердых веществ в жидкой среде и получение коллоидных систем. Коллоидные системы отличаются тем, что распределенные в жидкости частицы твердых веществ не осаждаются под действием земного притяжения, а остаются во взвешенном состоянии. При диспергировании происходят три основных процесса.
Речь идет о следующих процессах:
- Процесс диспергирования: Смачивание, разделение, стабилизация.
- Смачивание поверхности частиц твердого вещества жидкой средой
- Механическое разделение и измельчение ассоциированных частиц (агрегатов и агломератов)
- Стабилизация возникших в результате диспергирования новых, более мелких частиц и предотвращение их повторного слипания (флокуляции)
Процесс смачивания частиц твердого вещества и их стабилизации для защиты от дополнительной флокуляции зависит от взаимодействия между твердой и жидкой фазами.
![]() |
![]() |
Эффект Doughnut
Наилучшие результаты диспергирования смеси на диссольвере DISPERMAT достигаются в том случае, когда основные параметры процесса согласованы между собой: Геометрия и диаметр рабочей емкости, окружная скорость вращения фрезы и глубина ее погружения в смесь, а также реологические свойства смеси.
- Все зависит от эффекта Doughnut!
После смешения твердых и жидких компонентов смесь, вследствие повышения частоты вращения вала, должна находиться в равномерном вращательном движении (до полного исчезновения неподвижных зон). Получается воронка, внутри которой образовывается пустота, где видна середина фрезы. Это и называется эффектом Doughnut.
Этим самым Вы достигаете самое эффективное разрушение агломератов, которое происходит в районе движения фрезы. Эффект Doughnut образуется при ламинарном течении в тех случаях, когда смесь отбрасывается вращающейся зубчатой фрезой наружу к стенкам емкости, где поток разделяется на две части.
Нижний поток смеси устремляется к центру дна емкости под вращающийся вал, а затем снова поднимается наверх к зубчатой фрезе. Второй поток образует воронку, которая хорошо видна сверху.
Характер текучести воронки при эффекте Doughnut зависит от количества твердых компонентов в смеси. При пониженном содержании твердых компонентов вязкость смеси оказывается слишком низкой, что приводит к разбрызгиванию и вспениванию смеси. Кроме того, снижение механической энергии приведет к значительному ухудшению диспергирующей способности фрезы. С другой стороны, если содержание твердых компонентов слишком высоко, повышенная вязкость смеси в целом не позволяет добиться оптимального характера текучести. При этом образуется так называемая граница текучести, и смесь остается практически неподвижной. Как следствие, зубчатая фреза проскальзывает в массе или, в крайнем случае, вращается вхолостую.
3. Принцип работы фрезы по разрушению агломерированных твердых компонентов смеси
При вращении фрезы с повышенной скоростью перед ее зубцами образуется зона повышенного давления, а за ними – зона разрежения. Попеременное воздействие повышенного давления и разрежения на агломераты твердых частиц приводит к их разрушению.
Кроме того, зубцы фрезы оказывают также ударное действие на частицы смеси. Значительная часть работы по диспергированию частиц происходит также на верхней и нижней поверхностях фрезы. При скоростном вращении фрезы на ее поверхностях образуются вихревые потоки массы, в которых разрушаются агломераты твердых частиц. Вихревой поток, образующийся, прежде всего, на нижней поверхности фрезы, в значительной степени зависит также от расстояния между фрезой и дном емкости. При уменьшении этого расстояния интенсивность этого вихревого потока увеличивается. Благодаря этому увеличивается скорость потока между нижней поверхностью фрезы и дном емкости и геометрия в рабочей емкости появляется возможность увеличения скорости вращения диссольверного вала, так как в этом случае переход от ламинарного к турбулентному течению массы происходит значительно позднее.
Кроме того, благодаря увеличению частоты вращения вала становится возможным дальнейшее увеличение механической энергии смешивания, обеспечивающей эффективность диспергирования. Как правило, наилучшие результаты диспергирования достигаются в том случае, когда работа проводится с максимальной механической энергией смешивания без разрушения образующейся в емкости воронки (эффекта Doughnut).
Механическая энергия смешивания P (W) определяется по частоте вращения n (1/с) и вращающему моменту M (Nm) вала (π = 3,141.....).
P = 2π n M
Геометрия в рабочей емкости
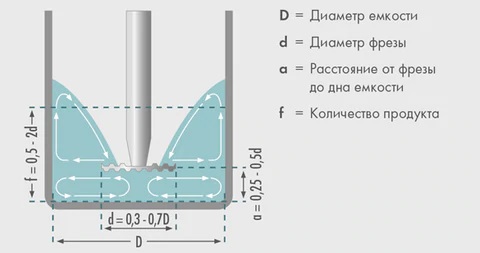
Окружная скорость вращения в зависимости от числа оборотов и диаметра фрезы
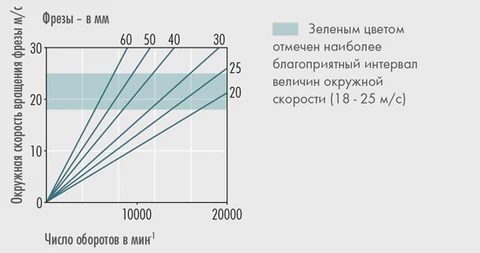
Рекомендуемый диаметр фрезы в зависимости от вязкости и размера рабочей емкости.
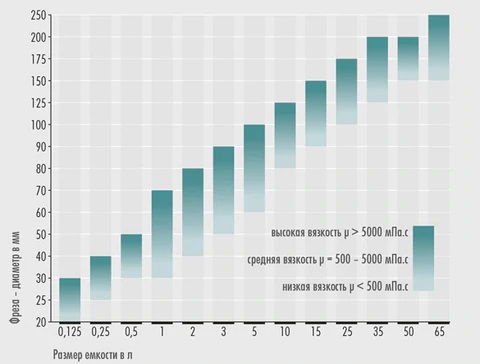
4. Метод работы и оптимизация состава смеси
Чаще всего на практике применяется следующая технологическая последовательность: Сначала в рабочую емкость вводят жидкие компоненты. Затем при медленном вращении вала порциями вводят такое количество порошкообразных компонентов, при котором с увеличением скорости вращения вала до 18 - 25 м/с происходит образование воронки (эффект Dougnut).
- Не надо бояться больших оборотов!
После предварительного перемешивания необходимо снять остатки смеси со стенок емкости и диссольверного вала. Только после этого проводится собственно диспергирование предварительно перемешанной смеси, при этом в диспергируемой массе должна образоваться воронка. При проведении этой работы следует использовать преимущества диссольверов DISPERMAT®. Не надо бояться высоких скоростей вращения вала! При использовании фрезы диаметром 25 мм вал диссольвера должен вращаться со скоростью 15000 мин-1, чтобы фреза могла достичь окружной скорости 20 м/с. Окончательный эффект диспергирования на диссольверах DISPERMAT® достигается через 10 - 15 минут работы. Дальнейшая работа диссольвера, как правило, не приводит к улучшению результатов диспергирования агломератов; как показывают анализы проб, устанавливается окончательный размер частиц. Если предъявляются повышенные требования к размеру частиц или к обработке агломератов, плохо поддающихся диспергированию, требуется применение мельницы.
5. Перенос лабораторных результатов в производственные условия
Одним из важнейших условий успешной работы является возможность переноса результатов диспергирования, полученных на диссольверах, в основное производство.
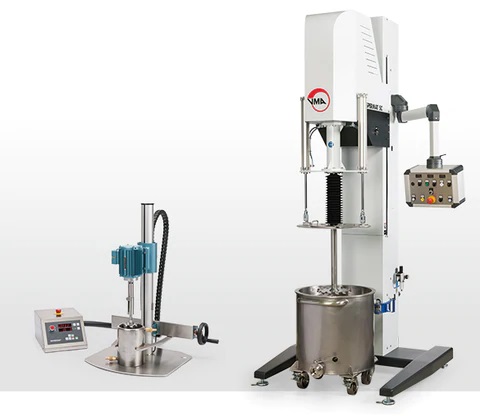
Ранее уже отмечалось, что результат диспергирования зависит как от движения агломератов вокруг зубчатой фрезы, так и от количества механической энергии, вводимой в смесь в емкости для диспергирования. Количество механической энергии является тем параметром, который определяет максимальный конечный результат разрушения агломератов, а движение агломератов определяет длительность процесса, которая необходима для достижения конечного результата диспергирования. Диспергирование агломератов происходит, как правило, в зоне действия усилий сдвига, которая образуется на рабочих поверхностях зубчатой фрезы. Величина образующихся усилий сдвига (оптимальные результаты диспергирования) определяется краевой конструкцией зубчатой фрезы, поскольку именно эта часть фрезы вращается в массе с максимальной скоростью.
По этой причине скорость (окружная скорость вращения 12 фрезы) может быть использована в качестве критерия при переносе результатов лабораторных исследований в производственные условия. Однако данное утверждение относится только к оценке конечного результата процесса диспергирования, но не к его длительности. В диссольверах DISPERMAT® конечный результат обычно достигается быстрее, так как в лабораторном диссольвере траектория движения агломератов до зубчатой фрезы короче, чем в промышленных диссольверах. Точное воспроизведение окончательных результатов диспергирования достигается в тех случаях, когда температура массы в лабораторном диссольвере соответствует температуре массы в промышленном оборудовании. По этой причине при работе с диссольверами DISPERMAT® рекомендуется использовать двухстенные темперированные емкости. Для достижения в лабораторном диссольвере такой же окружной скорости вращения фрезы, как и в промышленном оборудовании, вал лабораторного диссольвера должен вращаться постоянно и стабильно с повышенной скоростью. При использовании различных зубчатых фрез окружная скорость легко рассчитывается по вышеуказанной формуле.
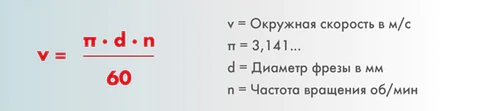
6. Окружная скорость вращения в зависимости от числа оборотов и диаметра фрезы
Ниже приведены три примера, на которых приведена зависимость окружной скорости от числа оборотов и диаметра фрезы. Зеленым цветом отмечен наиболее благоприятный интервал величин окружной скорости (18 - 25 м/с).
Пример для смеси объемом 100 мл, обрабатываемой на лабораторном диссольвере DISPERMAT®
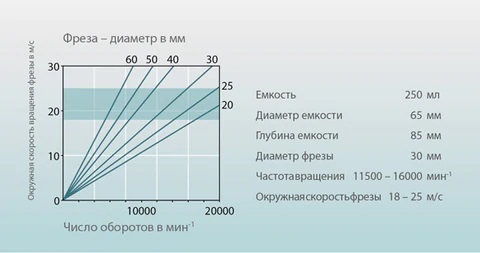
Пример для смеси объемом 2500 мл, обрабатываемой на лабораторно- исследовательском диссольвере DISPERMAT®
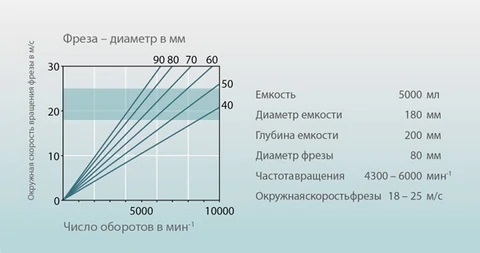
Пример для смеси объемом 30 л, обрабатываемой на лабораторно- исследовательском диссольвере DISPERMAT®
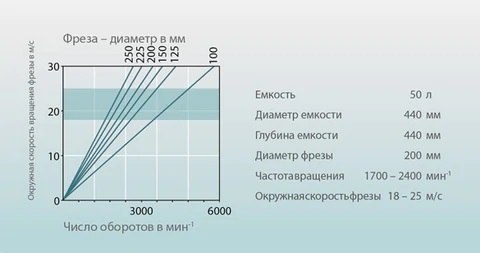
7. Что следует предпринять, если не достигнут желаемый Эффект диспергирования ?
В случае, если результат диспергирования не соответствует предъявляемым требованиям, необходимо проверить следующие параметры процесса:
![]() Длительность диспергированияДиссольвер позволяет достичь оптимума диспергирования в течение 10-15 минут работы. Продолжительность работы более 20 мин, не приводит, как правило, к улучшению результатов. |
![]() ФлокуляцияОбразование хлопьевидных агрегатов (флокуляция) из мелких частиц дисперсной фазы. Избавиться можно при помощи соответствующих диспергирующих добавок. |
![]() Эффект DoughnutВ течение всего процесса необходимо контролировать сохранение воронки. |
![]() ТемператураВ процессе диспергирования в продукт вносится энергия, что приводит к повышению температуры продукта. При этом движение потока продукта нарушается и отрицательно сказывается на качестве. В таких случаях рекомендуется использование рабочих емкостей с двойными стенками. |
![]() Частота вращенияПовышение частоты вращения вала (и тем самым увеличение окружной скорости вращения) позволяет вводить в смесь дополнительную механическую энергию, не разрушая эффект Doughnut. |
![]() Компоненты смесиВозможна частичная корректировка рецептуры с помощью замены компонентов. При этом надо помнить, что диссольвер предназначен для диспергирования, а не для размола компонентов. Диссольвер не может разрушить первичные частицы вещества. |
![]() Геометрия емкостиИзменить расстояние между фрезой и дном емкости. |
![]() ВакуумДля минимального попадания воздуха в продукт рекомендуется прорабатывать высоковязкие продукты под вакуумом. |
![]() Количество смесиУменьшить или увеличить объем смеси. |
![]() АддитивыПри помощи добавления различных аддитивов можно значительно улучшить и ускорить процесс диспергирования и качество. |
![]() ФрезаПрименять фрезы различного размера. |
![]() Содержание твердых компонентовДилатантное течение потока смеси загустевающего при добавлении сухих компонентов не влияет на эффект Doughnut. |
8. Реологические свойства смеси
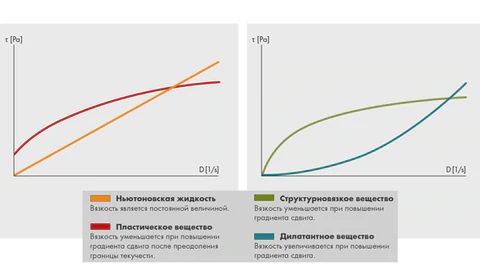
Для достижения оптимальных результатов диспергирования необходимо контролировать реологические свойства смеси. К сожалению, реологические свойства нельзя охарактеризовать одним параметром, например, только вязкостью. Вязкость представляет собой способность вещества растекаться под действием внешних усилий сдвига и подвергаться необратимым деформациям.
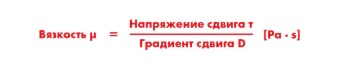
Коэффициент вязкости, часто называемый просто вязкость, зависит от свойств вещества и определяется как соотношение касательного напряжения сдвига и скорости сдвига. Только в ньютоновских жидкостях вязкость является постоянной (например, в воде, минеральных маслах). Все другие жидкости, не имеющие такого свойства, называются неньютоновскими, они встречаются гораздо чаще. В рецептурах смесей используются сложные по реологическим свойствам вещества. Для их характеристики используются такие термины, как кажущаяся вязкость, пластическое поведение, граница текучести, тиксотропия, реопексия и дилатансия.
общевзятый диапазон вязкости:
низкая вязкость μ < 500 мПа.с
высокая вязкость > 5000 мПа.с
средняя вязкость μ = 500 – 5000 мПа.с
9. Диспергирование в вакууме
При диспергировании с помощью диссольвера воздух часто попадает в диспергируемую смесь. При использовании веществ низкой и средней вязкости воздух удаляется сам уже во время или, в крайнем случае, после процесса диспергирования; часто этому способствует введение в смесь добавки. Однако при использовании продуктов с более высокой степенью вязкости и пределом текучести (см. также «Реологические свойства смеси») воздух, попавший в смесь, не всегда выходит наружу.
В данном случае процесс диспергирования должен обязательно осуществляться с применением вакуума во избежание попадание воздуха и микропузырьков, которые могут проникнуть в используемую массу через мельчайшие поры и отверстия в поверхности. Кроме того, часто необходимо применять скребковую систему для счищения диспергируемой смеси с внутренней стенки емкости и доставки ее в центральную часть емкости. Благодаря такому подходу в процессе диспергирования будет задействован весь загруженный материал.
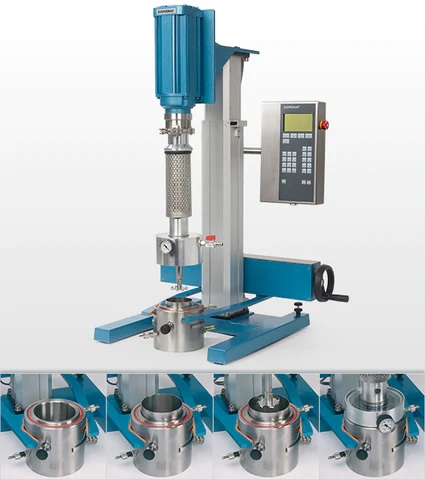
Основные преимущества вакуумного диспергирования:
- Возможность получать высоковязкие смеси без пузырьков воздуха
- Образование пены сводится к минимуму, особенно в водянистой среде
- С применением вакуума можно легко получать продукты, которые вступают в реакции с образованием кислорода или влажности.
- При вакуумном диспергировании качество продукта (тонкодисперсность) заметно выше